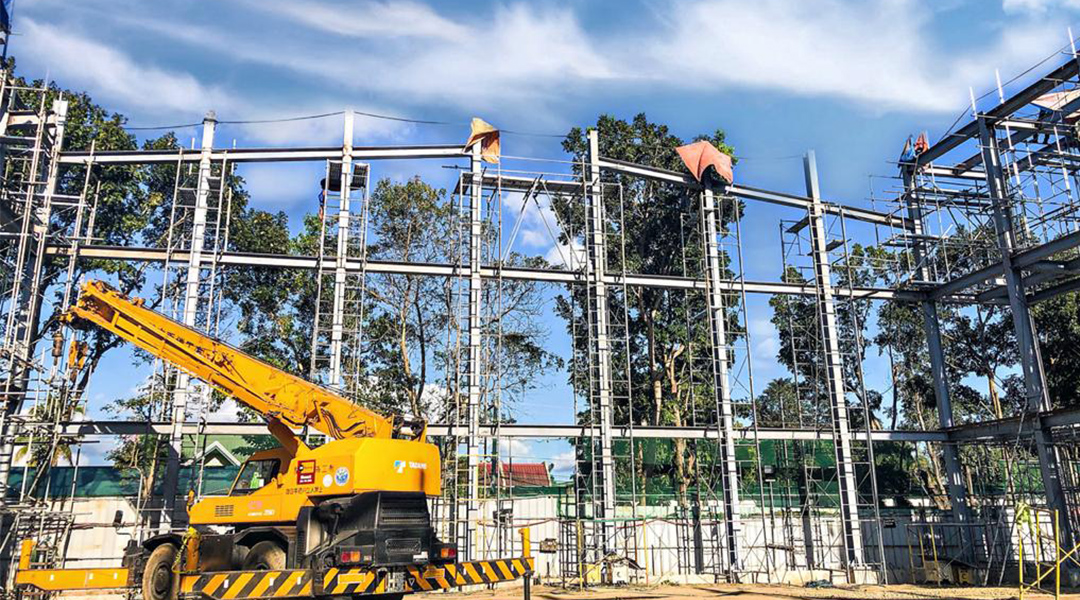
Construction Trends: Building Impactful Changes in the New Normal
As with most design trends, construction trends are paving the way for impactful changes in the industry. As the Philippines prepares to shift to the new normal, the construction industry will also need lasting solutions to sustain the momentum of economic recovery.
Previously for our e-mag issue, co-CEO of MC Geometric Proportions, Inc. co-CEO Mike Lagman shared with BluPrint his company’s strategy for thriving during the pandemic. Apart from the three R’s (relationship, responsibility, and retention) that served as the pillars of the company he co-owns with his wife Charmaine, he also mentioned the challenges and pitfalls that loom over the construction industry. This year, however, will be marked by enduring efforts. He says these will not only mitigate ongoing challenges, but also revitalize the industry as a whole.
In another discussion with Lagman, we once again called for his expert insights and perspectives. This time, he weighed in on the trends, methodologies, and realities that are currently shaping the Philippine construction industry. He tells us which of these will become more commonplace, what technologies are proving to be revolutionary for the industry, and where the country is now in terms of putting sustainability into practice.
Mike Lagman Charmaine and Mike Lagman
When it comes to construction technology trends this year, what are the biggest changes we’ll see? What are causing or leading to these changes?
As a rule, tech trends follow the intricate demands of each situation. This year in construction, we will see a shift to long-term adaptations to the pandemic once thought as merely a one-off.
Efficiency for reducing waste and maximizing space will be the norm as the limits of the workforce have turned from temporary crisis management to an inevitable reality. We should then expect to see more emphasis on modular, prefabricated, and offsite construction.
What are the latest construction technologies or methodologies that we can expect to become widespread in practice this year? What advantages do they bring?
Offsite fabrication is easily going to become more widespread in practice. If it worked in the early pandemic, making the process more efficient for today’s social distancing protocols is an efficient limitation, with great potential for the future’s post-pandemic period. Having offsite locations for building components allows installation timing to be rigidly controlled and more ready-to-build, as there is more emphasis on quality control before shipping to the site.
A lot of the advantages of this approach has to do with foresight. You can address an error of an onsite fabrication is on site because of the convenience. But if it’s offsite, the potential mistakes need to be foreseen and prevented. Knowing this, more emphasis on quality control is intrinsically instilled into the project at all stages. It’s a definite plus. It complements the need for efficiency and responsibility in the workplace, with pandemic protocols in place already limiting manpower density.
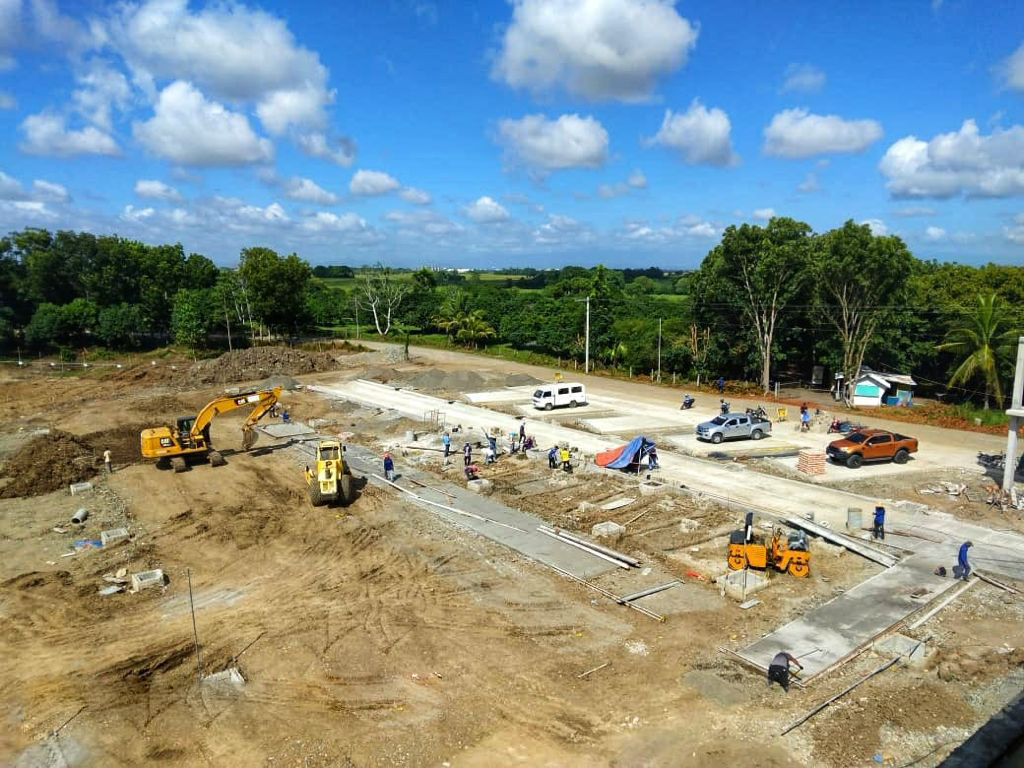
How far along is the Philippines when it comes to construction technologies for green/sustainable architecture? What are the current challenges or setbacks that the construction industry is currently experience in this area?
The Philippine Green Building Council and the DOE have launched the Philippine Energy Efficiency Project to promote energy efficiency and sustainability in buildings. So far, however, we only have seven certified green buildings in the whole country. These are ARYA Residences, Unilever Bayanihan Project, Bench Tower, CITI Plaza, LLADA Building, Paseo Verse at Real, and Zuellig Building.
We are making progress but the obstacles to development comes primarily from cost, culture, and their interrelation. While cost for green architecture is to be expected as being more expensive, the lack of a movement in advocacy (especially government) for the public sphere for green architecture’s long-term benefits stunts its growth. The emphasis primarily needs to be on its financial pay offs in the long term, as well as the pragmatic benefits to the entities that will use the buildings. Among these are cooler temperatures and less electricity consumption. Also, these need to be coupled with environmental awareness.
Augmented Reality (AR) is among the technologies currently being explored for construction applications. How do you envision this happening in the Philippines?
It is true that the future of augmented reality in construction is going to be bright here in the Philippines. While the software is being enhanced, I already have my technical team study the different software available and compare which is the most suitable for my company.
Fortunately, we can already see a wide range of AR software being used abroad. This, I believe, will not go unnoticed by the rest of the construction milieu. As this pandemic forced construction firms to work remotely and adopt digital solutions, the construction industry faces positive disruption with AR software. We are now preparing to take advantage in key stages.
While the technology becomes more accessible, AR will initially be utilized in construction’s human resources. Clearly, merging the real world with the virtual comes at the behest of man’s ability to integrate the two. Priorities in human resources for construction will thus be centered on project planning and team collaboration. Knowledge of safety training, especially asynchronously, can be better understood with more realistic scenarios.
Real-time project planning will be enhanced in presenting, implementing, and completing a project in all its stages. The digital plans can be virtually superimposed against the project in situ. Engineers, architects, and clients can take full advantage of this in terms of modifying projects through the use of a detailed AR display that’s accessible and calculated. This reduces risk of having to perform major rework as the project is going along.
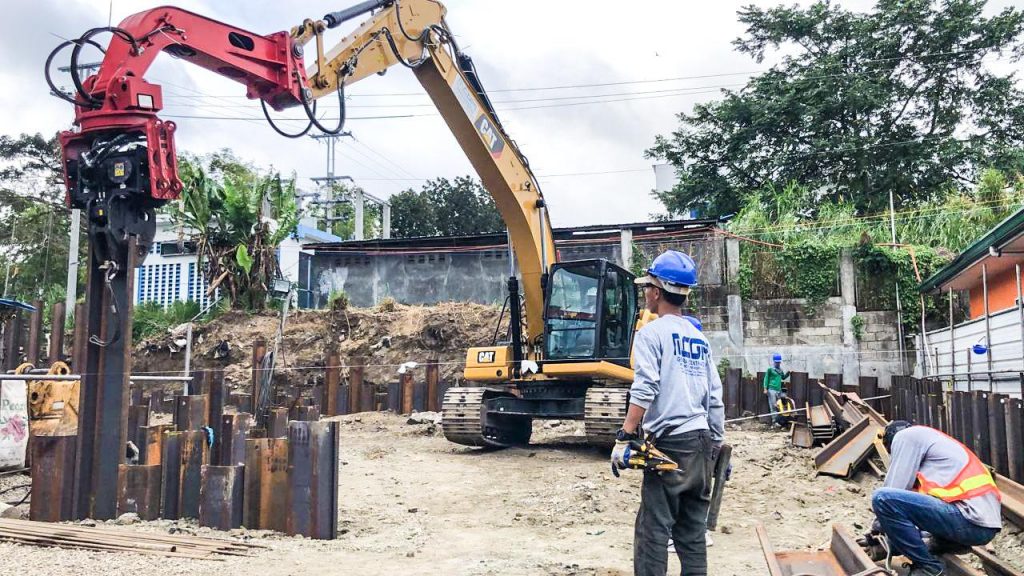
Lastly, what are your insights about the modular construction technologies in the Philippines? We already saw some interesting examples last year, but do you think it will start becoming commonplace this year? What are the most common misconceptions about them?
I think that modular construction represents the times we’re living in right now – modular and transitional. Likewise, it also suggests the attitudes we should be cultivating – adaptable and sustainable. In the Philippines, construction entities will start to implement it more regularly. They will realize that modularity is more efficient, faster, and ultimately more cost-effective.
Traditional structures’ tried and tested familiarities are becoming more and more overshadowed by modular construction’s advantages. While made from the same materials, they are collapsible and can be reconstructed elsewhere. As with any new technology risk, uncertainty and fear all factor into its misconceptions. Because it’s collapsible, some may see it as temporary, low quality, or unsustainable. On the other hand, new technology is also misconceived as necessarily expensive which is not always the case.
Photos courtesy of MC Geometric Proportions, Inc.